Avec l’évolution des techniques constructives, le marché du prémur est aujourd’hui particulièrement porteur dans une logique de mix produit où systèmes préfabriqués et banches traditionnelles peuvent cohabiter en parfaite intelligence.
En France, plusieurs entreprises se sont déjà développées pour pouvoir répondre à la forte croissance de la mise en œuvre de prémurs, dont notamment KP1, Rector, Fehr ou encore Spurgin.
Le prémur est un élément de structure préfabriqué industriellement composé de deux parois minces en béton armé reliées et maintenues espacées par des raidisseurs métalliques. Le vide (7cm mini) entre les deux parois (généré par la dimension des raidisseurs) est rempli de béton sur chantier.
- Dimensions max: 3,30 X 12,30 m
- Épaisseur des parois : 4,5 cm* à 7,5 cm
- Poids : 250 à 350 kg/m²
- Coupe-feu : 0 h 30 à 4 h 00
- Epaisseur standard : 16 cm* à 40 cm Procédé de fabrication
*suivant les fabricants, la gamme peut commencer à partir de 18 cm (parois 5,5 cm).
Procédé de fabrication
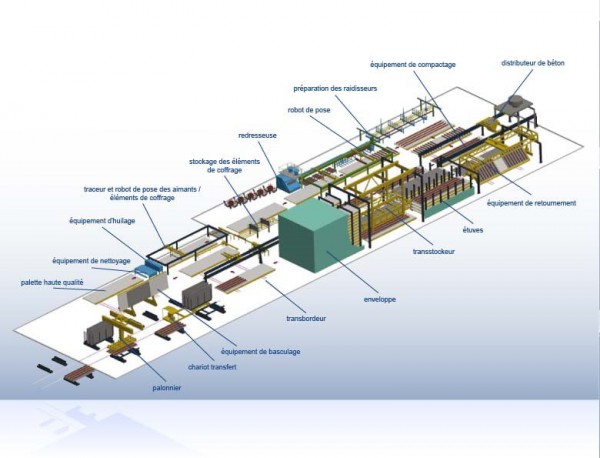
Schéma de principe de l’usine de préfabrication.
L’unité de fabrication fonctionne avec des tables coffrantes métalliques qui se déplacent automatiquement d’un poste de travail à l’autre.
- 1ère étape : Tracé du voile sur la table coffrante métallique par la pose de joues métalliques aimantées
- 2ème étape : Découpe et mise en place des aciers (barres HA, raidisseurs, crochets de levage) et implantation des boîtes de réservation.
- 3ème étape : Coulage et vibration de la 1ère peau. La vibration et le contrôle du coffrage métallique permettent de maîtriser le bullage et la qualité du parement.
- 4ème étape : Mise en étuve de la 1ère peau pendant environ 8h.
5ème étape : Pour la 2ème peau, répétition des étapes 1, 2 et 3. Puis, acheminement et retournement de la 1ère peau qui vient se placer en face de la 2ème peau fraichement coulée. Ensuite, le complexe est vibré et mis en étuve.
- 6ème étape : Stockage sur rack et chargement sur camion
Inconvénients
Prix : la mise en œuvre de prémur nécessite une mise au point en phase étude. Dès le départ, il faut être vigilant aux PV à intégrer dans le chiffrage parce que cela peut engendrer rapidement des surcoûts rendant le prémur non rentable financièrement.
Planning « études »: il faut créer une bonne interface entre le BET et le BE du fabricant pour gérer les possibilités (ou impossibilités) techniques mais aussi et surtout le planning (temps d’étude plus long). D’autant plus que toute modification est impossible en phase de fabrication. De même pour les CES et notamment l’électricien. Il est important de prendre en compte l’incidence en Frais de Chantier puisque l’utilisation de prémur diminue la location et l’achat de matériel. C’est en intégrant cette incidence dans le comparatif financier que l’on obtient une bonne idée du surcoût (ou non) de la solution prémur.
Stockage : la solution prémur nécessite d’immobiliser une zone pour le stockage. Deux types d’organisation sont envisageables pour la mise en œuvre de prémur:
1. Isolement d’un espace accolé à l’aire de livraison permettant le stockage du rack (1.5m x 9.4m) où sont disposés les prémurs. Dans ce cas, les prémurs peuvent être mis en place au cours de la journée. Cette zone de stockage doit être identifiée et sécurisée ; en effet, le rack chargé peut atteindre un poids de 22t. Enfin, il est important de placer cet espace en fonction de la capacité de levage de la grue.
2. Immobilisation du camion du fabricant sur l’aire de livraison (emprise 2.5m x 55m) le temps de décharger et mettre en place les prémurs. Selon les conditions de chantier, l’immobilisation du camion peut être plus ou moins longue, ce qui peut engendrer une refacturation au chantier du temps d’immobilisation.
Cas des prémurs « grande hauteur » : la pose de prémur en grande hauteur (environ ≥ 3.0 m suivant fabricant), il faut réserver une aire spécifique où sera installé un retourneur, objet indispensable pour redresser le prémur.
Limites structurelles : certains éléments structuraux (poutres voiles, éléments en console) peuvent s’avérer difficiles à réaliser en prémur.
Contraintes de mise en œuvre : d’une part, le traçage et l’implantation des attentes doivent être réalisés avec précision pour obtenir un bon alignement des prémurs lors de la pose. D’autre part, le coulage du prémur se réalise en plusieurs fois pour éviter l’éclatement des parois sous la pression du béton.
Avantages
Sécurité : à tous les stades du « processus prémur », il existe des systèmes pour la sécurité. Les besoins en matériels sont beaucoup moins importants (banches notamment), seuls des TPS suffisent pour le maintien des prémurs. L’espace de travail est ainsi beaucoup moins encombré et donc
Planning « chantier » : ce type de produit permet de soulager ou d’améliorer la cadence et ainsi de réduire le délai GO. C’est un procédé facile et rapide à mettre en œuvre qui peut également permettre de gérer les périodes d’intempéries (fabrication en usine moins sensible aux conditions météorologiques).
Mise en œuvre : en terme de conditions de travail, il y a moins de matériel donc moins d’efforts physiques et de pénibilités. Nous utilisons également moins d’huile de décoffrage ce qui diminue de surcroît les risques sanitaires. La légèreté de ces panneaux (par rapport à un voile préfa) permet d’utiliser moins de panneaux pour une même surface et donc de limiter la saturation de la grue.
Qualité : l’utilisation de prémur permet d’obtenir une qualité de parement irréprochable. Il est très adapté au projet avec des finitions « brut ». De plus, en termes de finitions, seuls les joints entre prémurs restent à réaliser (économie en finition et ragréage).
Points singuliers : la souplesse d’utilisation du prémur permet de s’adapter aux difficultés du site. Ainsi, les prémurs peuvent s’avérer très utiles pour les pignons contre mitoyen ou en façade en limite de propriété. On peut également envisager de réaliser les voiles de grande hauteur ou les voiles dans un encombrement réduit (noyaux ascenseurs, gaines techniques).
Au premier abord, le prémur semble être un outil de construction couteux. En effet, par rapport à un voile de façade ou un voile intérieur standard, l’investissement ne sera pas rentable. De plus, il peut être inadapté au niveau structurel (poutre voile, éléments en console,…). Cependant, il trouve rapidement son intérêt dans bien des cas et notamment pour des opérations sujettes à des contraintes de délais, de mise en œuvre ou encore d’espace sur chantier.